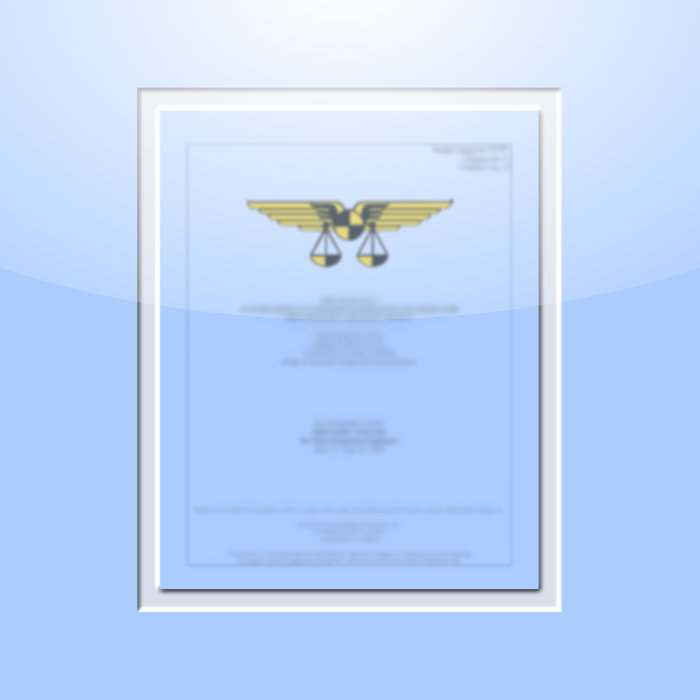
1610. Error Analysis of System Mass Properties
$20.00
SAWE Members get a $200 store credit each year.*
*Store credit coupon available at checkout, click the button in your shopping cart to apply the coupon.
Not applicable to SAWE textbooks and current conference technical papers.
Paper
Abstract
Objective of this analysis is to verify the margin of system mass properties over values sufficient for support of other required system capabilities, flight dynamics control, for instance. The system nominal mass properties characteristics are designed (with a tolerance over requirements) using imperfect knowledge of mass and location of its constituent elements. The effect of element errors is to induce net errors in calculated system mass properties. Direct measurement of system mass properties is impractical.
Approach. Considering both element-internal independent C G errors and element externally dependent alignment errors, a differential analysis calculates effect of net element errors on system mass properties. Then a combination of element effects shows total system error, which quantizes probable loss of system margin. The following information about the whole or portions of the system is provilded:
1)Standard deviation of the various mass properties parameters of the selected configuration.
2)Relative system-error contributions of the mass elements (ranked).
If item (1) shows net system uncertainty values which compromise satisfaction of system mass properties requirements, then item (2) shows which elements are the principal causes of the problems. They are considered cost-effective candidates for more stringent analysis or measurement of local element mass properties. The system error analysis is then rerun with the improved (tighter) element error inputs, and its output determines the best available (hopefully adequate) system mass properties margin.
Application of this work is to the Galileo space craft system. The system consists of a non-spinning (stator) portion, and a spinning (rotor) portion with long heavy radial appendages. Some of the system mass property design constraints are: retention of CG near the spin axis while matching rotor pitch and yaw moments of inertia; minimizing stator products of inertia; and maintaining margin between rotor spin inertia and overall system yaw inertia.
Operation of the analysis and of preliminary input processing are performed by computer. Acquisition of local element mass properties and alignment uncertainties, and loading input files turnout to be a significant part of the work. The programs can accommodate changes in mass distribution modeling.
Conclusion: Operation to date appears consistent, with preliminary inputs.