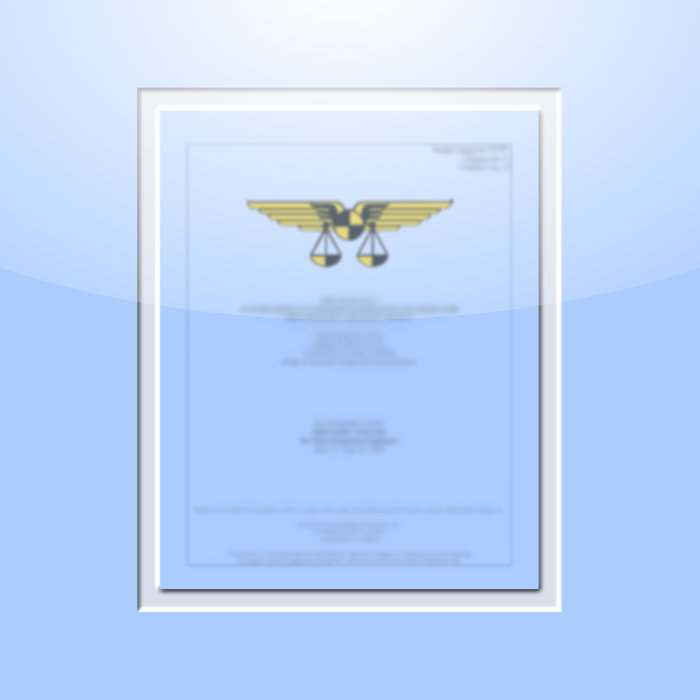
3547. Implementation of a Tool Chain for Extended Physics-Based Wing Mass Estimation in Early Design Stages
$20.00
SAWE Members get a $200 store credit each year.*
*Store credit coupon available at checkout, click the button in your shopping cart to apply the coupon.
Not applicable to SAWE textbooks and current conference technical papers.
Paper
Abstract
The state-of-the-art methods in preliminary wing design are using models employing physics-based methods for primary structures while using empirical correlations for secondary structures. Using those methods, detailed optimization as e.g. rear spar positions or flap size is only possible within a limited design space. Novel structural concepts such as multi-spar flap layouts or the introduction of composite materials cannot be analyzed using statistical methods and require extended higher level structural modeling. Therefore an interdisciplinary tool chain is developed for extended physics-based wing mass estimation. The tool chain consists of the following components: one central model generator, a structural finite element model, a structural sizing algorithm and loads models for aerodynamic, fuel, landing gear and engine loads. The structural finite element wing model consists of the following main parts: wing box, fixed trailing edge devices, movable trailing edge devices, spoilers, landing gears and engine pylons. The model generator is able to create several different kinds of track kinematics, covering most of the track types used in state-of-the-art aircrafts. To make the complexity of the model generation process feasible for one aircraft designer, a knowledge based approach is chosen. Therefore the central model generator requires a minimum set of easy-to- understand input parameters. This enables the aircraft designer to focus on the design and not on calculating input parameters. To include the tool chain in a wider multidisciplinary aircraft design environment, the aircraft parameterization CPACS (Common Parametric Aircraft Configuration Scheme) is used as central data model for input and output. The developed tool chain is implemented as flexible as possible to enable the designer to analyze also novel structural concepts or wing configurations. On wing configurational level, the tool chain can handle most types of different wing concepts, such as e.g. blended wing bodies, strut-braced wings and box wings. On the structural concepts side, the tool chain is able to handle various different rib and spar layouts and different materials (incl. composites).